Plastic plays a practical, often life enhancing, role in our lives. The word plastic – derived from the Greek word plastikos (meaning to mould), shapes our everyday world.
Plastic has come a long way from the Bakelite resin patented at the turn of the 20th Century that revolutionised how many consumer goods were mass-manufactured. Lightweight, durable and easy to work with, like many resins today, it could be moulded into an infinite number of shapes. With more than 85,000 listed plastic materials, and more than 45 polymer families, Thomas Catinat, operations manager at Broanmain Plastics, explains some of the common compositions and characteristics of materials that start in pellet form.
Plastics are essentially atoms that are grouped together to form molecules called monomers. These monomers link together to create polymers. That’s why ‘poly’ features in so many plastic materials names.
Polymers all offer varying degrees of strength, resistance, elasticity and even special features such as anti-bacterial or UV protection. The choice will depend on the application, for example if it needs to withstand high or extremely cold temperatures.
Polypropylene (PP) is generally deemed the most versatile and popular material for most applications. It has a fairly high melting point, can withstand daily wear and tear and is resistant to cracking and stress, even when flexed. For this reason, it’s often used in packaging applications, such as snap on lids or bottle caps, or medical tubing.
When replacing metal components with plastic, PP can be used to reduce weight providing the component won’t be put under a high level of stress. When high mechanical resistance is needed, a stronger polymer, such as Nylon or a Glass Fibre filling might be used.
Another good feature of PP is, like other thermoplastics, it can be melted down again to create new products. For example car parts, storage boxes, plastic pallets and even garden furniture.
Acrylonitrile Butadiene Styrene (ABS) is also relatively inexpensive and has a good impact and chemical resistance. For this reason is often used for visual parts, such as computer keyboard keys, televisions, plug sockets and even children’s play bricks.
Standard ABS is usually mixed with the most appropriate additives to make them cleaner, safer, stronger and shinier. Common examples include colour pigments, anti static agents and heat stabilisers.
Nylon isn’t just for stockings! In fact Polyamide Nylon (the most common PA66) has a very good chemical resistance so it is used as another replacement for metal in applications that require high strength, toughness and weight reduction, e.g. automotive parts. However, it’s worth keeping in mind that Nylon plastic can absorb moisture, which in softer polyamide products can affect the dimensional stability.
Polycarbonate (PC) was used to make the astronaut helmet for the Apollo landing in 1969. In everyday applications today, its low weight, impact resistance means that the material is used for parts that require clear lenses or windows, from car headlamps to visors, medical device cannulas and cellphones. PC is also used in a lot of safety gear used by professional sports athletes, such as the outer shell of ski helmets. Acrylic (PMMA) is an alternative, although the material is not as strong as PC.
Thomas emphasises the importance of seeking a moulding partner that can think creatively and use their engineering acumen and chemical knowledge to present the best materials for a moulding project. “Understanding how the molecular structure of plastics change as they are processed is critical when considering which material to use for your project,” ends Thomas.
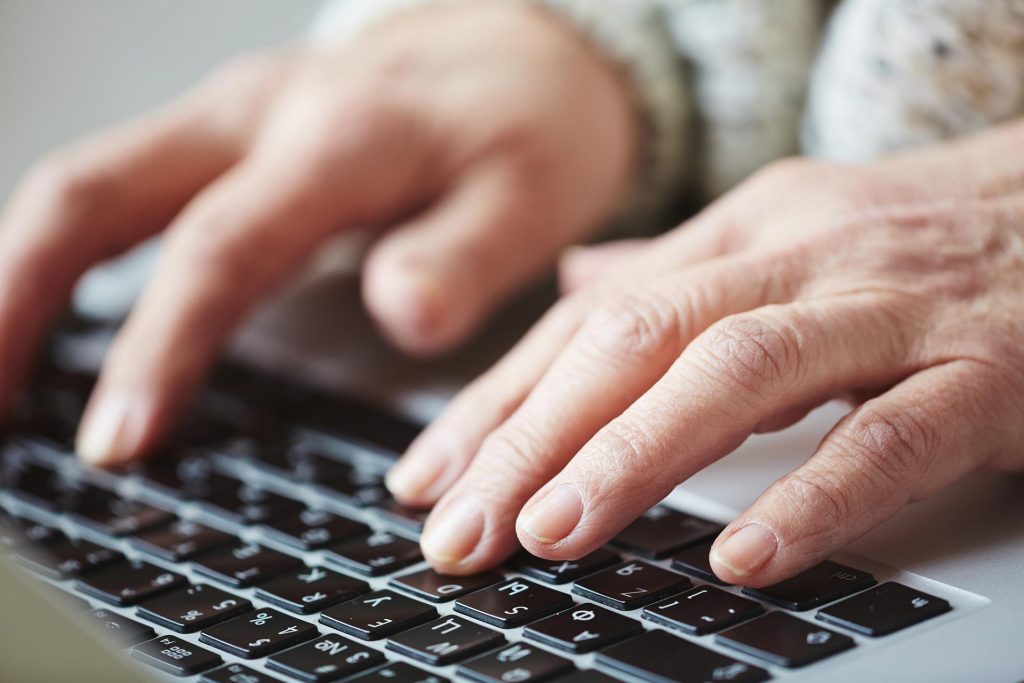
Acrylonitrile Butadiene Styrene (ABS) has a good impact and chemical resistance so is often used for visual parts, such as computer keyboard keys

Image 2: Polycarbonate used to make the astronaut helmet for the Apollo landing is today used in parts that require clear lenses or windows, from car headlamps to the outer shell of sports helmets

Image 3: Using colour pigment additives ensures that decorative features run through the entire product
Broanmain Plastics is a specialist family-owned technical trade plastic moulder and one of only a few UK plastic moulders to offer thermoplastic, thermosetting and injection moulding from one facility. Founded over 60 years ago, Broanmain supports a wide range of industries from aerospace, electronics and defence through to the science sectors and consumer goods, and supports customers with prototype development, tool trials, right through to high volume production runs.
Broanmain Plastics, Forge Works, Horsham Rd, Dorking RH5 4EJ